Maximizing Profitability through Iron Ore Beneficiation: Unlocking the Potential of Lean-Grade Ores
Bhubaneswar (Odisha) [India], July 10: The global demand for high-quality iron ore is increasing, prompting mining corporations to look for new ways to extract and treat this valuable resource. By eliminating gangue materials, the beneficiation procedure increases the iron levels in the concentrate. Sree Metaliks Limited, a major player in the iron and steel sector, [...]
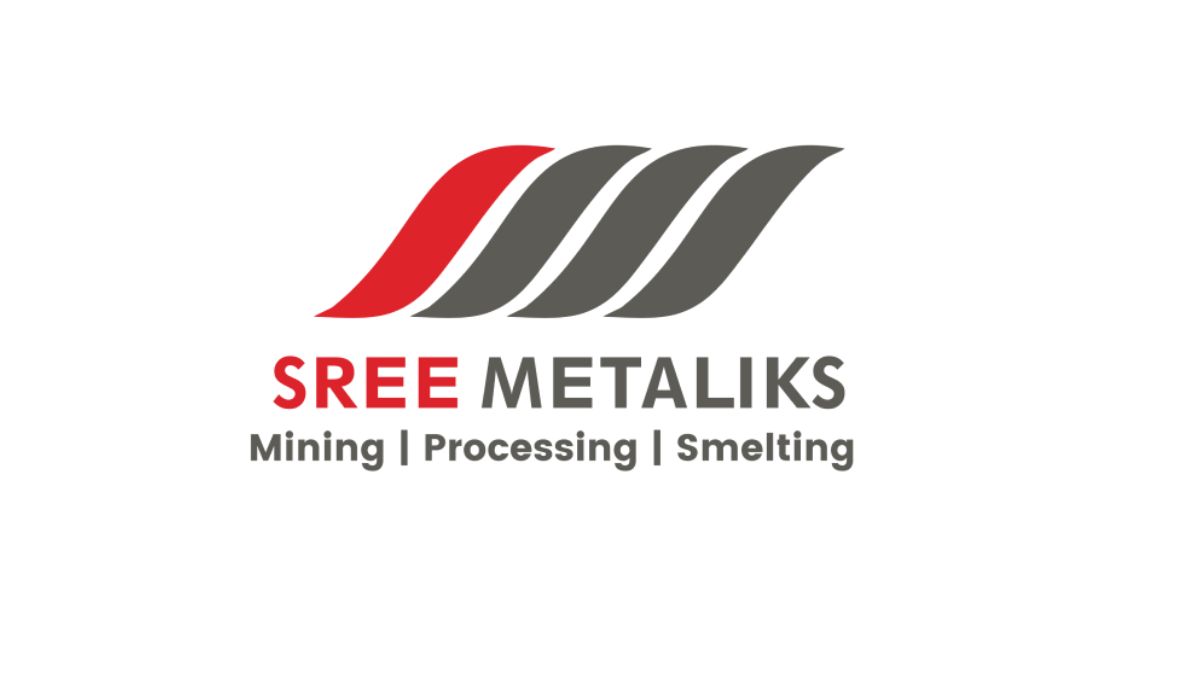
Bhubaneswar (Odisha) [India], July 10: The global demand for high-quality iron ore is increasing, prompting mining corporations to look for new ways to extract and treat this valuable resource. By eliminating gangue materials, the beneficiation procedure increases the iron levels in the concentrate. Sree Metaliks Limited, a major player in the iron and steel sector, has used innovative physical beneficiation methods to boost overall efficiency. This article discusses the significance of iron ore beneficiation and the procedures used by Sree Metaliks to maximize profitability.
The Significance of Iron Ore Beneficiation:
The concentration of the desired mineral extracted from the ore determines the profitability of a mine at its core. Alumina and silica are the most common contaminants in iron ore. Impurities in mineral phases found in iron ore include kaolinite, gibbsite, and quartzite. Hematite and goethite are the most common iron phases found in iron ore. Alumina and silica are reduced through the beneficiation process utilizing various techniques, such as gravity and magnetic separation, based on their physical qualities. The concentrate obtained by physical beneficiation should be appropriate for use in the blast furnace, DRI, sinter, and pellet manufacturing processes, all of which will eventually be used to create steel.
The Iron Ore Beneficiation Process:
The ore is brittle due to its goethetic-hematite composition. It is connected with clay minerals and contains a significant quantity of natural fines from iron ore mining. To enhance lean-grade iron ore fines, SreeMetaliks uses a thorough iron ore beneficiation process (wet process). Because the ore contains natural fines and kaolinite, the scrubbing technique is used to remove slime (below 100 m) before sending the grinding unit. The lean-grade ore is washed and sorted into different-size fractions using a drum scrubber and a vibrating screen. The coarse fraction is jigged to generate DRI feed material. The -5mm size fraction material is again classed at 1 mm and beneficiated to generate sinter feed materials utilizing an advanced gravity separation process (in an advanced fine jig with high frequency and reduced amplitude). The rejected materials from the gravity process and the -1 mm size fractions are pulverized in a closed circuit ball mill employing a hydrocyclone and a high-frequency screen. The ground product, along with the slimes, is treated using a wet high-intensity magnetic separator (WHIMS) to enhance the Fe value for the preparation of pellet feed materials. The non-magnetic portion is finally rejected as tailings.
Results and Benefits:
The beneficiation method adopted by Sree Metaliks has yielded amazing results. Initially, hematite iron ore fines with Fe contents ranging from 55 to 57% are treated to produce a concentrate with Fe contents ranging from 61-62%. This superior concentration is appropriate for the production of high-quality iron ore pellets. While tailings are lost at a rate of 20-25%, they still contain roughly 38-40% Fe and can be repurposed to make value-added products or further recover iron values using advanced processes such as the reduction roasting process.
Key Advantages of Iron Ore Beneficiation:
Hazardous Material Elimination: Sree Metaliks’ iron ore beneficiation process prioritizes environmental sustainability. It eliminates the usage of toxic products, ensuring worker safety and reducing the impact on adjacent ecosystems.
Water Conservation: With an emphasis on responsible water management, Sree Metaliks’ beneficiation process assures low water loss, leading to sustainable water consumption and conservation.
Beneficiation allows for the efficient utilization of lean-grade iron ore fines that would otherwise be judged inappropriate for iron production. Sree Metaliks maximizes the exploitation of precious minerals while reducing waste by upgrading these ores.
Productivity Increase: The increased concentration of iron obtained by beneficiation has a direct positive impact on the productivity of iron-making plants. Higher-quality feedstock benefits blast furnaces, DRI facilities, and sintering operations, resulting in increased energy and material efficiency and lower costs.
Iron ore beneficiation is critical to the mining industry’s profitability and sustainability. Sree Metaliks has successfully increased the iron content of lean-grade ores while minimizing the use of hazardous materials, conserving water resources, and lowering the carbon footprint in downstream plants through the production of high-quality concentrate.
“The new beneficiation process complements our existing techniques and enables us to increase the iron content of lean-grade ores even further.” We can extract even more valuable materials and reduce waste by leveraging this method, leading to a more sustainable mining approach,” said Mr. Kalyan Maity, Director of SML.
For More Information: https://sreemetaliks.com/
If you have any objection to this press release content, kindly contact pr.error.rectification[at]gmail.com to notify us. We will respond and rectify the situation in the next 24 hours.